Contents
- Index
Calculating Mold Cavity Dimensions
A mold cavity must be cut oversize to allow for the expansion of the mold cavity as it is raised from room temperature to casting temperature and the shrinkage of the alloy from the temperature it becomes a solid in the mold cavity until the alloy is at room temperature
This process begins with a bullet designed with linear and radial dimensions set to the desired values of the as-cast bullet when cast from a specified casting alloy.
From the bullet design data entry form, click the menu item titled "Calculators" at the top of the form to open the
"Mold and alloy expansion coefficient calculations" Module.
1. Select the mold material. The software will display a contraction coefficient that is associated with the mold material.
1. (a) A custom mold material may be selected and the associated contraction coefficient entered.
2. Select the casting alloy. If a custom alloy is selected, the percentages of tin and antimony, by weight, will need to be entered.
3. Enter or edit the optimum casting temperature of the mold.
4. Enter the ambient or room temperature of the mold and the as-cast bullet when measurements are taken.
5. Click the "5. Calculate the Cavity Diameter Coefficient" button.
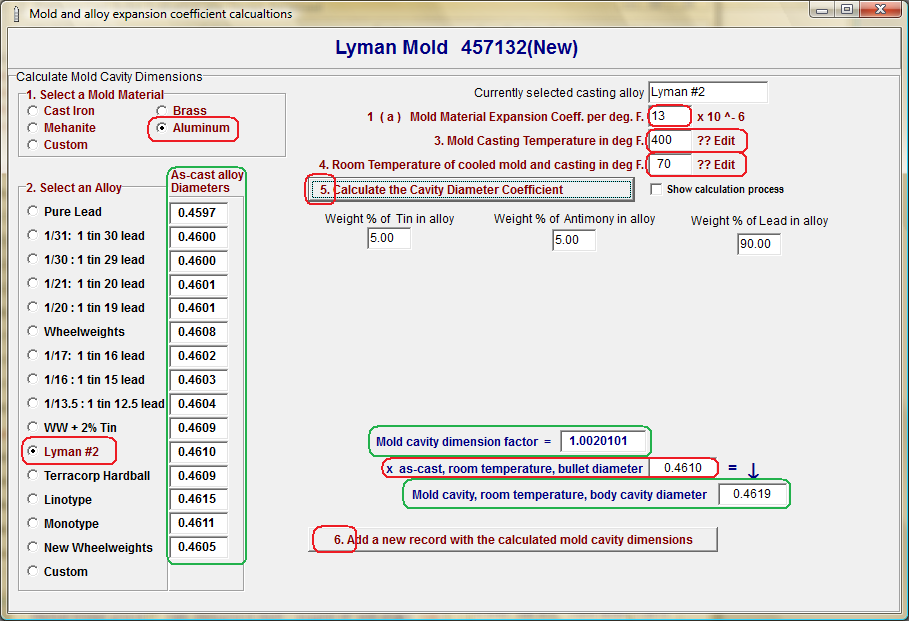
The software will calculate the temperature at which the alloy becomes a solid and also the contraction coefficient of the casting alloy.
The casting alloy contraction coefficient is then multiplied by the difference in temperature between alloy solidification and room temperature.
This product, when multiplied by and added to, the dimensions of the bullet, will determine the dimensions of the casting cavity at the optimum casting temperature of the mold.
The mold material contraction coefficient is multiplied by the difference between the optimum mold temperature and room temperature.
This product, when multiplied by and subtracted from, the dimensions of the hot mold cavity, determines the dimensions of the mold cavity at room temperature.
Checking the
check box will display the algorithms and values in the calculation process.
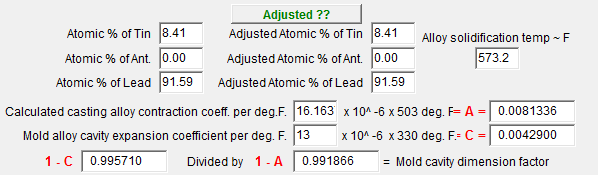
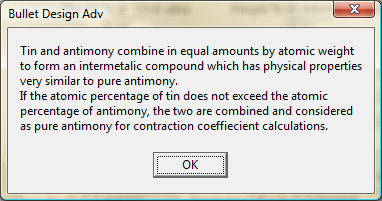
The room temperature, cavity dimensions divided by the as-cast, bullet dimensions returns a "Mold cavity dimension factor"
The software will also calculate Predicted As-cast bullet diameters when different casting alloys are used in the mold with the calculated cavity dimensions.
When the
button is clicked, the software will multiply all of the selected bullet design dimensions by the dimension factor and create a new bullet design record with those values. The new record will have the same name and description as the old record but the bullet number will have the text "CAV'" added.
The increased values of nose diameter, meplate diameter and ogive length will also alter the length of the ogive radius.
The Calculate Ogive form will open with the values of the bullet dimensions entered.
If you wish to maintain the same bullet dimension ogive radius when the mold cavity dimensions are cut, click the "Load Values" button to load the values of the mold cavity dimension and, edit the ogive radius, ogive length or meplate diameter as needed.
After clicking each "Calculate" button to change the dimension values, click the "Send Bore Ride Length and Tip Dia values to Calculations" to write the new values into the Bullet Cavity Record.
The software will create a new record with all bullet dimensions increased to create a mold cavity that should cast a bullet with the correct dimensions.
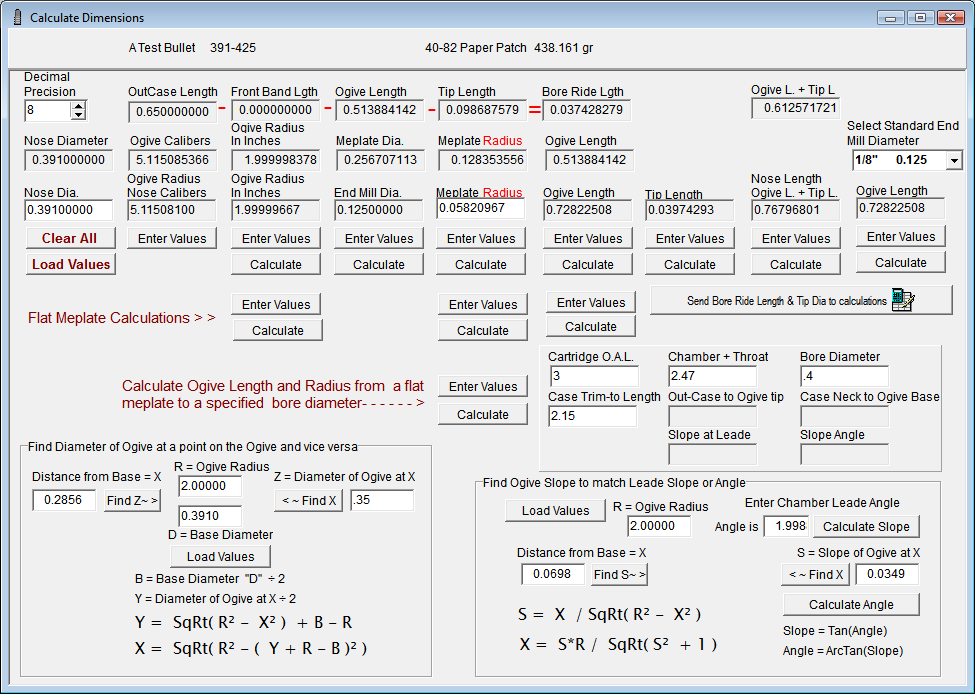
Copyright ©, TMT Enterprises 2012